The Collection
This section describes the colour category system. This followed by description of each category including equipment associated with it and how to use it. Then complicated/bespoke examples (NG6337 etc) and finally how to prepare the collection for loan. This will include all the casing stuff plus a description of the relationship with KSL.
Introduction[edit | edit source]
The National Gallery’s collection of art consists mainly of western European paintings from the 13th century to the beginning of the 20th century. The collection does include some sculptural objects, but the painting collection is its primary focus. Within this area of paintings are a wide variety of works with differing physical characteristics. These vary from early renaissance frescoes and panels (on a range of wooden supports) to many works on canvas and works on paper.
These works vary enormously in terms of mass and durability. For example, the collection includes very large and complex altarpieces, constructed from large wooden sections that can weigh up to 500kgs, to works on paper such as the Leonardo cartoon which are extremely ephemeral and require specific handling and display solutions. Paradoxically, large works of significant mass are themselves extremely vulnerable to movement by virtue of their structure working against the material they are made of when they are manipulated.
The role of the art handling department is to create safe systems of operations that we can use when moving the collection for any purpose. Any system that we develop needs to be understood by the art handling team as well as being reliable and repeatable. It also needs to follow the best conservation practice as described to us by our conservation team at the gallery.
The need for repeatable systems is due to the volume of moves that are undertaken each year with the collection. On average, around 15,000 moves of art works occur within the site of The National Gallery each year, all undertaken by the art handling team. This covers all aspects of our work, including basic moves throughout the gallery site, thousands of separate installations and preparation of works from the collection when loaned to other museums throughout the world.
Our aim is to create working systems that can safely cope with this volume of work whilst also being measurable. This is very important for the standard of our work as though we do create individual solutions to specific problems, we also need to know that our team is operating within a well understood framework from which we can confidently make decisions about the work in our care.
To facilitate our approach to the collection, we have developed a technical classification system that describes the art handling requirements for each individual object within the collection. This system breaks the collection down into three categories and names each category after a colour, either yellow, blue or silver.
Each of the categories assumes some simple characteristics for each object. Essentially weight and size are the main determining factors, the record of which category a work is placed in can be found on the individual record for each artwork held in the main collection database (TMS) under the art handling section. Within this record further, more detailed information can be included (please refer to the database description for further information).
The use of a largely generic classification system then allows us to design specific handling solutions to each category. In turn, the problems of handling and installing a specific object can be seen within this framework. The nature of the collection at the gallery has meant that such an approach is possible since the movement of large numbers of works that have similar physical characteristics is essentially the same. It also means that specific, individual solutions can be found to unique problems that can be seen within the context of the main framework.
A crucial element to the system is to develop the correct equipment alongside the correct process and approach. The art handling department has a long-standing equipment development program (now more than 20 years old) that designs and has manufactured specific equipment relevant to each of the categories.
It is worth noting that we apply the same or similar approach to our exhibitions where possible, however the requirements of lenders and the type of objects that may be included in our shows means that a more variable response is often necessary (please refer to exhibitions). This though can still be referred to the general principals established by our system. In the following pages we describe the processes and equipment for each of the categories.

Colour Category System[edit | edit source]
Due to the nature of the picture collection at The National Gallery, it is possible to categorise paintings according to the actions necessary for de/installation. This has led us to group works into three categories for this purpose, which are as follows.
Although there are exceptions to these categories, nearly every object in the collection can be group in one of these sections. Our approach to designing installation and transportation solutions is informed by this system.
Standard Manual Lift or Yellow Move
The yellow move category encompasses the simplest moves we are required to undertake. The category includes all works that can be manually handled over small distances by two art handlers, or can be installed without the need for additional equipment to elevate the painting into position.
The category does not necessarily state the characteristics of the works it includes but generally it refers to paintings weighing under 60kgs. The size of the work is also not such a significant factor as quite large paintings can be included if it is determined they fall within the ease of handling required.
The yellow category contains around 60% of the works within the gallery's collection and will form the majority of moves throughout the year. Using the correct equipment associated with the category (as listed below) multiple moves of paintings can occur simultaneously and this is frequently found to be the case when large gallery hangs occur. Commonly the works within the category are installed using a plate system or The National Gallery gadget system (please refer to installation methods) and additional security measures are also applied at installation.
Medium Lift or Silver Move
The silver move category covers most of the mid-range installations and moves that we undertake. This category probably accounts for around 20 to 25% of all moves that occur and requires the use of a minimum of three art handlers plus the designated equipment (as described here).
For these moves, we set a limit of 150kgs in weight for the object being moved. Most of the works that fall into this category also tend to be large in area with a major dimension usually exceeding 2 metres.
A lower weight limit is not set as the category considers the physical dimensions of the paintings involved as well as their weight. Often, we find canvas paintings can be light enough to fall within the yellow category but of such dimensions as to create significant problems when manually handling them.
Works within this category are usually transported singularly on stacker trolleys (see equipment). There are a variety of hanging methods employed when installing these works though the most common are supporting brackets and plates or a suspension system (within the National gallery chains are employed). Usually, given the size of the works, standard security is employed when on display.
Heavy Lift or Blue Move
The Blue move category encompasses the largest and most logistically challenging objects within the National Gallery’s collection.
The most common example of works found in this category are the group of large altarpieces dating from the early renaissance section of the main Collection. These works are usually the heaviest pieces, being up to 500kgs in weight but are also very large objects in surface area with a complex construction.
Conservation issues within the altarpieces can also be significant and therefore this category includes a number of bespoke handling solutions to individual objects (see the additional projects described in this section including for NG1).
The category also includes all the largest canvas works found in other sections of the collection. These works are not necessarily significant in weight, but it has been determined that their scale precludes their inclusion in the silver category and therefore they fall within blue moves.
Large moves described by this category are not an everyday occurrence, however, moves of all category of works have increased significantly over the last few years and the biggest volume increase has probably been within this section. In total, works within this category account for around 10% of the main floor display but when moved can account for a significantly greater percentage of the Departments resources and time. For example, NG1 (described elsewhere in this section) takes around 3 days to reposition and the majority of the AH team to carry out this task.
Yellow Equipment
As the works associated with this category can be manually handled within the short distances of a gallery or packing room, the equipment required consists of two forms of transportation necessary to move these paintings across larger distances within the two main buildings that make up the National Gallery.
The first and most common piece of equipment used for this purpose is the NG standard Picture Trolley. The standard picture trolley is a medium sized transportation trolley that is used for a large variety of moves and also for temporary storage in the Gallery’s stores. The original design was created by the department more than 20 years ago and consists of 4 units. The design, though generic in nature, was conceived to allow the best ease of movement throughout the Gallery site whilst also maximising the carrying capacity of the trolley. Its durability is such that it can also be used to carry works outside of the yellow category.
Part of the working philosophy of the team is that our art handlers carry only a very minimal amount of equipment on their person (basically a tape measure and standard screwdriver). The yellow trolleys have therefore been designed with a storage capacity for other tools and hanging equipment. This consists of two draws which are located at either end of the trolley.
The yellow trolleys are a standard, daily use piece of equipment which have served us well for many years. However, in keeping with our habit of revising our equipment and improving where necessary, a new design has been developed by one of our team supervisors with the first production model recently delivered. Here is his description of the new design and how it differs from the original model.
Yellow Trollies
The yellow trollies are key to how our teams operate in the gallery and the opportunity to re-think the design was not only a chance to make some physical modifications but also an opportunity to reconsider how we use them and make positive changes to our working practice. The trollies are used for the majority of picture movements, rehangs and exhibitions so the primary aims of my design were to increase the capacity for carrying multiple works, improve access throughout the gallery and to provide teams with the correct tools and fixings for each job.
The original design was very successful and the physical changes I made were relatively minor. I added a horizontal extension allowing us to transport larger paintings, slimmed the overall width of the trolley by 50mm to make it easier to pass through doorways, gave it radial corners to remove the sharp edges and increased the clearance around the wheels allowing us to fit brakes. The trolley itself is made from aluminium rather than the original steel design with a 3mm steel deck replacing the 18mm ply and weighting the bottom to ensure stability and provide the necessary weight for the vibration dampening function of the wheels. For the overall structure I reduced the distance between the two outer uprights which both increases the ability to stack paintings side by side but also increases the central space on the deck for items that need to travel flat.
Working across a large site such as the National Gallery one key issue is ensuring that teams have the right tools and hardware ready to hand for each job. We try to minimise the equipment carried by individual technicians and so the majority of our fixings, screws and tooling are kept in the two drawers of each yellow trolley. Maintaining stock and making sure everything goes back in the right place can be difficult during busy periods and a regular frustration for our teams is tracking back and forth across the gallery in search of missing items. For the new trolley I have designed a removable insert for the fixings drawer. The intention is to provide two inserts for each trolley with fixings specific to the two different hanging systems we work with; either hanging from chains or screwing fixings directly into the wall. Through the act of collecting the right drawer insert for each job I am hoping that the process of acknowledging the contents and stock before setting off will become automatic, thereby reducing the frustration of finding items missing. The inserts also double as a tool box that can be removed for easy access during installs and to be restocked at the end of each day.
Alongside the project of designing the trolley we also repurposed a small existing storage area to function as a tooling station and essentially a garage for the trolleys to be stored in. This area has become key to the function of the new trolley design and intended usage, it puts all of the stock, tooling and resources in one place and the layout is arranged specifically around ease of access with a work bench for storing and stocking the drawer inserts. Providing a space for the trolleys to be returned to at the end of each day and collected from every morning may seem incredibly simple but working across such a large site with multiple picture stores and two tooling areas represents a subtle but fundamental change to how we think about the trolleys and how we use them on a daily basis
Tom Hemming, Team Supervisor
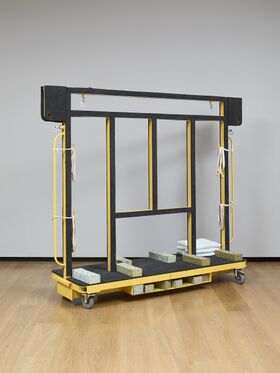
Picture Bin
The second type of transportation equipment used for yellow moves is the picture bin. The concept for this consists of any kind of box on wheels able to carry small works by placing dividers between each work to allow “bridging”. The department has designed a standard National Gallery picture bin and has two units available to it. However, it is possible to quickly and easily produced this equipment, constructed from MDF or wood and ply and have at least another 10 units made in this way that were produced during temporary periods of very high picture movements (for example emptying stores). The bins are also very useful as temporary storage units where small works can be safely held and accounted for within a proper storage facility.
Unlike the yellow trolleys, there is obviously a physical limit to the size of the works that can be held within a bin. Normally this tends to be paintings with a major frame dimension of no more than 75cms, the works will also be required to weigh less than 25kgs each.
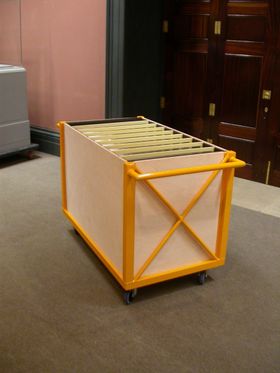
Silver Equipment
The two primary pieces of equipment used in this category of move is a standard, 2000kg manually operated hydraulic stacker (maximum platform height of 4.5ms) and the National Gallery stacker trolley, designed by the department for this purpose. The aim of the stacker trolley is to transport the painting to the installation site and then be attached to the manual stacker so providing the lifting power to install or de-install the work. This operation removes most of the manual handling of the work itself, so providing a good health and safety option for the department as well as improving basic preventative conservation needs when transporting larger paintings within the gallery.
This type of equipment, from the original prototype, has been extensively remodelled and improved over a number of years through the creation of 7 different models or Marques. This includes designs which relate to specific roles necessary in the gallery or specific objects in the collection. For example, the Leonardo Cartoon is displayed using a specially reinforced, glazed steel box. This weighs about 190kgs so nominally would take it outside the silver category. However as this is the most efficient method we have of installing the work then a specific stacker trolley was created for this role.
When using this method of transportation and installation, it is often necessary for team members to work at height. Therefore,
the third piece of equipment associated with the category is a MEWP, working at height runabout. The type we use is the Genie GR 12. This piece of equipment needs to be versatile and sensitive enough to work around the stacker trolley set-up and we have found it has almost completely eliminated the use of step ladders within the procedure, an original goal of the process design.
The original concept for the equipment came from one of our senior technicians and the following statement by him describes how a prototype design was first agreed:
Silver Trolley
We have been using our stacker trolleys for 16 years now and they have proved a unique and practical way of undertaking the installation of large paintings within The National Gallery's collection. They have also become indispensable to the installation of smaller paintings at height in galleries where the pictures are double hung.
The story about how they came into being, highlights how the art handling department has been able to gain inspiration to create new methods of working, through visits to other Institutions around the world. For example, while helping on the de-installation of the Dennis Mahon exhibition up in Edinburgh in 1997 I noticed that the technicians there were using table tennis tables which could be folded up and moved around on wheels for packing and unpacking works of art. Our portable packing tables at the time were by comparison heavy, cumbersome and time consuming to move. As a result, we sourced our own table tennis tables and have been using them ever since as have a growing number of other galleries around the world.
This brings us back to the stacker trolley. On a courier trip to the Alte Pinakothek in Munich in November 1999 with a large full length portrait by Van Dyck, I witnessed the conservators (who also doubled as the art handling team there) place the painting face in on a large wooden A frame trolley, which was taken up to the galleries after the conservation check had been completed. Once the position for the installation had been established two of the team went up ladders on either side and a third member proceeded to pick up the whole A frame with a genie superlift stacker. The trolley was steadied by the two staff members up the ladders as it rose to the height at which the picture was to be hung. Once at height the two technicians hooked up the picture to the wire hanging system which was used throughout the gallery, unstrapped the painting and slowly lowered the A Frame while the technicians supported the picture allowing it back to the wall gently as the A frame descended. I was struck by how little additional handling was needed and how easily the installation had proceeded.
Consequently, on returning to The National Gallery I suggested we might try and develop a trolley which would be designed solely for this purpose. We had just had our own in house designed regular picture trolleys fabricated for us by a firm up in Tamworth near Birmingham and were confident they would be able to make these new trolleys for us.
It took roughly two and a half years before we were in a place where finances and time came together to allow us to start designing the first National Gallery stacker trolleys. The initial idea had come from my courier trip to Munich, but it was Patrick O’Sullivan who was to undertake drawing up the design along with solving the nuts and bolts issues creating a new trolley like this required. We discussed the features a bespoke trolley of this sort should have, and Patrick incorporated these into his design.
Like our new picture trolleys, the stacker trolleys were to be adjustable giving them as much flexibility over the sizes of pictures they could accommodate as possible. They were designed with a top bar which could extend both vertically (like our regular picture trolleys) but in addition horizontally on both sides. Patrick also designed two raised, padded feet which were attached and could slide along an aluminium bar which ran the length of the base of the trolley and gave adjustment to accommodate the decorative mouldings and carvings on the large variety of picture frames they would be employed to support.
He also designed the wheelbase to slide back when the trolley was lifted off the ground, either to install or de-install a painting. This meant that the padded feet could be brought right up to the wall making it possible to lift the picture straight off or onto the wall brackets from the trolley in most situations. They could then be slid back into position before being lowered to the ground giving the trolleys maximum stability for moving around the gallery when loaded, with large pictures.
Also, unlike the A frame in Munich which was just lifted from underneath by the stacker. These trolleys had a compartment designed into the framework underneath which snugly housed the tines of the stacker. There was also a bar which allowed the stacker and the trolley to be coupled together giving us the insurance the trolley could not slip of the tines with a painting in situ.
In 2004 the first prototype stacker trolley arrived at the gallery and proved itself invaluable in the day to day work of the art handling department. We discovered that not only was the trolley making the installation of large paintings easier for art handlers, but it also gave the curators a secure way of viewing a painting against the wall before settling on the height at which they intended to hang it.
The process before this involved padding out the tines of a stacker. Lifting the picture off a trolley manually and balancing it on those tines while it was precariously lifted into position. If especially large, one or two technicians were needed up on ladders to keep the balance at the top of the painting.
Now, a picture could be brought into position and lifted to the desired height without the added complication of ladders and technicians obscuring the view of the painting on the wall. It also often resulted in less handling for the pictures as they can be stored temporarily on the trolley until they were needed again.
Six months after the arrival of the first prototype we added another two improved versions of the first prototype to our growing collection of in house designed equipment. We eventually donated the original prototype to The National Museum Cardiff and have replaced the two trolleys which arrived after it with new improved versions, all of which were designed by Patrick.
We now have eight stacker trolleys, including two smaller units for installing smaller paintings at height. (One of which has been designed to double up specifically for the installation of Leonardo da Vinci’s Cartoon NG6337. ‘The Virgin and Child with Saint Anne and the Infant Saint John the Baptist.”)
Wheel units no longer slide but swivel and several of the units have top bars which only lift vertically. Between them they cover most of the paintings within the collection that are better suited to being stackered into position rather than lifted manually. They are also regularly used as temporary storage units helping us to keep down the manual handling of large paintings to a bare minimum.
All in all, our stacker trolleys have proved an indispensable tool in the safe handling of large paintings. They continue to aid us in the installation, movement and storage of our larger paintings with an ease and simplicity we could hardly have imagined when the department started back in 1992.
Danny Metcalf Senior Art Handler
Blue Equipment
As this includes the most technically challenging works in the collection, the process and equipment used to move these objects also tends to be the most complicated. The main piece of equipment used in a blue move is the blue hoist. This item is essentially a large lifting and transportation device that also includes a significant working at height capability and several features to ease the operation and protect the object in transport.
Essentially though the concept for the blue hoist is very similar to the silver categories stacker trolley. In keeping with our general approach to large equipment within the Gallery site, the design of the blue hoist is modular. As with the stacker trolley, the lifting “engine” of the hoist is provided by a standard, 2000kgs stacker which marries with the hoist in a similar way to the Stacker trolley. The use of this approach has meant that the design could originally be more easily developed by the department as more complex elements, such as a hydraulic capability, could be ignored. The design also includes two working at height access towers that join with the main hoist body to provide access for the team. Tower outriggers (as found in standard mobile scaffold platforms) are not necessary as the main body of the hoist provides the stability. These towers can be swapped out for the GR12 MEWPS accordingly, at least one MEWP always being needed to perform other functions with the hoist.
The design also includes a movable tyne system that is arranged in all three axis allowing the position of the hoist to be replicated for each move whilst the tynes go and “grab” the object. In addition, two “picture clamps” are situated at the top of the hoist. These can be adjusted to take into account the width of a picture (up to a maximum of 5.5 metres) and are used to hold the painting vertically when the works are moved (something vital for the moving of altarpieces).
The hoist has eliminated the need for manual lifting of the largest objects in the collection, however the operation still involves a significant use of the teams’ resource with at least 6 technicians required for a blue move.
In addition to the hoist, blue move equipment also includes other items such as the picture carrying “towers”. These are large, triangular shaped carrying scaffolds that are used to move objects through specific routes of the Gallery or to free the use of the blue hoist, allowing multiple blue moves in one session (something that has become more frequent).
Equipment[edit | edit source]
The art handling department deploys several general and bespoke pieces of equipment to carry out our role. Our approach has been to develop the processes and concepts for our tasks and then to match the equipment to our needs. This has led to a significant design program within the department over many years that has resulted in original design solutions and models of equipment that have then been improved upon. These include the following:
The Standard Picture Trolley
Associated with the yellow category move, our standard trolley was first developed in 1998 as a general-use piece of equipment assigned to art handling teams. The trolley is durable enough to transport all categories of pictures within the collection but is primarily used to transport multiple works simultaneously. The trolley also has the capacity to safely carry tools and materials for the team whilst transporting pictures. The original design has recently been upgraded to a new model by Tom Hemming, one of our team supervisors.
The Stacker Trolley
Associated with the Aluminium move, this picture trolley is used to transport and install larger category works. It is designed for one painting at a time and links with a hydraulic stacker to ease installation for the team. This design has undergone several modifications and variants.
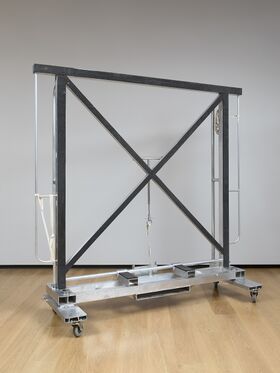
The Case Roller
This piece of equipment was developed by the team to facilitate the unpacking of paintings from their cases. Most picture cases (used for external transport) must be laid flat to be unpacked and this usually requires a significant physical effort. The case roller acts as a quarter round lever and preparation table that makes this operation significantly easier.
The Blue Hoist
The blue hoist is a large, multi-functional picture transporter and installer that we developed to deal with the largest works in the collection. It is designed to register with our altarpiece display system and has features such as adjustable picture clamps made to hold a work in perfect vertical orientation for transport.
We also use a large range of common equipment normally found within art handling teams. These include J bars for cases, mobile packing tables, skoots and skates, weigh pallets and for working at height we use Mobile Elevated Work Platforms or MEWPS.
The standard model MEWP we use is the Genie GR12. This model has the right weight to height ratio necessary for our gallery environment. We have two of these and they have completely replaced the use of ladders and made redundant the use of scaffold. Step ladders are still occasionally used under normal, health and safety protocols.
Complicated Installations[edit | edit source]
As mentioned in our category system, the art handling department adopts a three-part system of classification for each artwork in the collection. The blue category includes the largest and heaviest works that also provide the biggest technical challenge to us. Most of these works are large altarpieces or canvases that exceed the limits imposed on the other categories, and special equipment (namely in the form of the blue hoist) has been developed to deal with these moves.
However, there are several moves that can be considered exceptionally significant even within the terms of the blue category and these we call complicated installations. This category of move usually requires further processes or equipment designs to be developed, including some intervention to support the object itself. Usually this is due to the fragility of the object involved with respect to its size but can also be due to display requirements, such as a particular framing approach. A good example of this category is the requirements for the large painting by Sebastiano del Piombo The Raising of Lazarus (NG1).
NG1 is a painting with significant conservation issues around its structure that have caused considerable problems when it was necessary to move the work. The picture was originally a large altarpiece painted on a thick wooden support (exact nature unknown) which was then “transferred” during the 18th century whilst in the possession of the French royal court. The transferring process simply involves removing the original wooden support and replacing it with a canvas one. However, over time this caused significant conservation issues and when it became the responsibility of The National Gallery art handling department to move it (late 20th century) the process necessary to do so was too precarious to carry out without risking damage to the painting. A new process was necessary and would involve designing a support system for the painting which could then work with the newly designed blue hoist.
New structural support for NG1
We had already adopted a possible solution in other altarpieces. This involved designing an aluminium “cage” that would fit around the painting as a permanent feature. This would then replace the picture frame as the standard support for the work, meaning the painting could be safely de-framed (necessary for NG1 in particular). In addition, a system of four “screens” was designed that could attach to the new cage. These would wrap around the front of the work where strategically placed soft pads would gently hold the surface of the work in place whilst it was moved (the main issue being the movement of the surface on the canvas). This support system could be applied whilst the work was hanging and would provide protection against the normal art handling techniques such as “bowling” (the re-orientation of a work from one axis to another). This also meant that the main display frame became a “veneer” for appearance only, as the structural load of the work was taken by the new support frame. With this arrangement, the work could now be de-installed and moved using the blue hoist system as described in the blue category.
Installing the new display frame
At the time of the development of the support system for NG1, we also discussed the possibility of a new display frame that would fit around it and reproduce the main altarpiece form its original location in a church in Italy. However, it would be several more years before this project began, eventually being realised due to the picture’s involvement in the gallery exhibition of Sebastiano and Michelangelo in 2017.
This project added another level of complexity to this move as it involved the installation of an extremely large frame in four parts, placed around the painting once the work itself had already been installed. To make this possible we developed an installation system that “registered” with the cage of the painting when installed.
The new systems have proved to be very successful and have allowed the painting to be moved as required (something we had stopped doing prior to the development of the process). However, it remains possibly the most complicated of moves necessary at The National Gallery, made more so by its very impressive display frame.
Patrick O’Sullivan, Head of Art Handling
Loan Preparation[edit | edit source]
As a department we are central to the loan programme and we work closely with several key departments including collection registrars, curatorial, conservation, framing and photography.
The loan process begins with the collection registrars who receive loan requests from museums and galleries across the world.
This in turn triggers a whole process. Art handling becomes heavily involved once a case order is received from one of the collection registrars. For over 25 years, we worked with Kent Services Limited (KSL) as a supplier of cases to the gallery, which we used to loan works from the collection. Sadly, in late 2020 they ceased trading. We now have a stock of cases they we purchased from KSL and we fit them out with Polyurethane open cell foam (grade S275) and Plastazote LD45 for each painting in the collection that goes on loan.
The case order form contains key information such as the medium, framed dimensions and conservation requirements. We use this information and some other vital details to allocate a suitable case from our stock. We may have to transport the case from offsite storage, then fit out that case, ready for loan. The last stage of this part of the process is to create an invoice for the borrower as they pay for the rental of the case for the duration of the loan.
Later in the loan process we schedule the removal of works from display that are going on loan. This will mean a minor or major rehang of that gallery and we liaise with the relevant curator in order to complete this work. They supply us with a plan, usually a visual document, and we check this and translate the details into TMS. This enable the art handlers to have a worksheet to work from and refer to. We also provide labels for each work, they are written by the curator in question but checked and printed by us, ready for the hang.
This hang is organised in advance and considers any conservation or framing work that needs to take place before going on loan. If a work is not on display it is moved from storage to conservation for pre-loan checks and for the work to be carried out.
We organise the packing of works and coordinate the presence of a Conservator in order to check the painting right before it is packed into the case. Finally, when the case is collected at handling is present for the moving and loading.
When a painting comes back from loan this process happens in reverse and we organise each stage of this process, liaising with, and physically moving the painting and rehanging it in the gallery.
Over the course of a normal year we loan approximately 100 paintings from the collection. Therefore, this process happens multiple times and on any one day there are several loans at various stages in this process.
Louise Marlborough, Administrator